编译 陈讲运
本文展示了由腐蚀引起的问题,并提出了新的可能解决方案以供讨论。

热水加热系统的主要部件通常由低铁或无合金的黑色金属材料组成,即所谓的黑钢。它的耐蚀性不是基于材料特性,而是基于在热水中不存在氧气或其他氧化剂。
VDI 2035-2是德国评估供暖系统腐蚀风险的最著名技术规则。一个更新的版本已经在草稿中。还有DIN EN 14868作为确定低于110°C的封闭水循环系统(包括冷却和冷却系统)中腐蚀可能性的指南,也必须遵守。VDI 2035明确地由腐蚀技术上封闭的系统制成,该系统没有明显的氧气转移,因此,欧洲标准还考虑了氧气系统。
氧气的作用
在所考虑的加热和冷却系统中,只要循环水的pH值在8到9的范围内,腐蚀过程就基本上取决于渗透氧气的量。原则上,氧化剂例如氧气的还原是必要的,以便可以不受阻碍地继续在金属材料上的溶解过程。酸-可以通过循环水的低pH值识别-也可以满足此要求。腐蚀过程的可能速度取决于其他水参数,以后会更多。
可以通过多种方式将氧气引入加热或冷却系统:
- 作为溶解氧通过填充或补足水(8至11 mg / l)。
- 从大气中,通过系统中的部分负压形成(通风机变成充气机!)。
- 通过水与空气的直接接触(开放式膨胀容器)。
- 通过有机材料I扩散(旧式地板采暖系统≠DIN 4726)。
- 通过有机材料II扩散(T> 40°C的增强软管)。
- 在维护或翻新过程中可能会产生气垫。
如果补给水中的天然氧气含量被腐蚀过程消耗used尽,则腐蚀速率仍可忽略不计,在整个系统使用寿命内,系统补给的系统体积不得超过系统体积的两倍,并且无法正常获取氧气。但是,在大型分支系统中,实际上很难做到这一点。
水对氧气腐蚀的影响
可能的氧腐蚀现象的程度和速度取决于几个影响因素。当然,主要因素是循环水中溶解氧的浓度,但硬度,pH值和电导率等参数也起作用。下面将对此进行更详细的研究。
氧气浓度
未经过氧气专门脱气或消耗的填充水含有8至11 g /m³的溶解氧。当与黑钢制成的部件发生反应时,最终形成磁铁矿(每立方米约36 g),同时氧浓度降至<0.1 mg / l。实际上,在密封的防腐蚀系统中测得的值为0.03至0.1 mg / l。的VDI 2035在这里被称为0.1毫克/升的限制,是可以预期的,低于该无损伤。但是,对于直接连接到区域供热的系统,必须遵守AGFW FW 510的更严格规格(0.02-0.1 mg / l)。
与腐蚀模型相对应,较高的氧气浓度也可以吸收更多的电荷(e-),这些电荷由正铁离子进入加热水中时逸出而留在金属上。
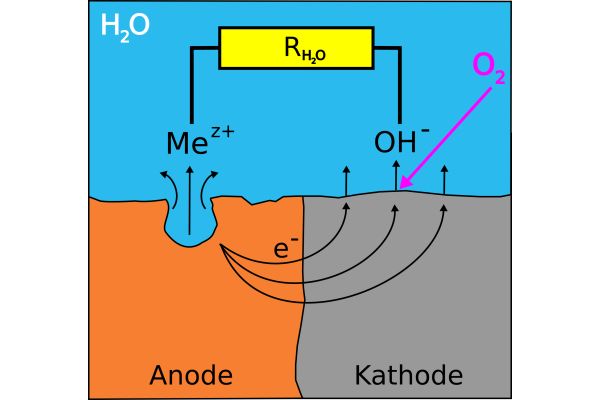
解释性模型,说明加热系统中存在氧气时黑钢的腐蚀过程。阳极和阴极表示同一钢体上发生金属溶解或氧还原的不同表面积。
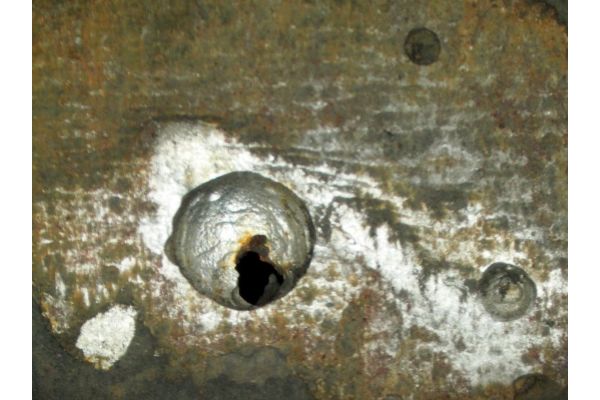
较旧的表面加热的蒸汽可渗透系统在两年内在热发生器上造成了此处所示的壁突破。
这种去极化是金属固体不受阻碍地溶解过程的先决条件,最终会导致部件失效或至少导致过多的磁铁矿形成。
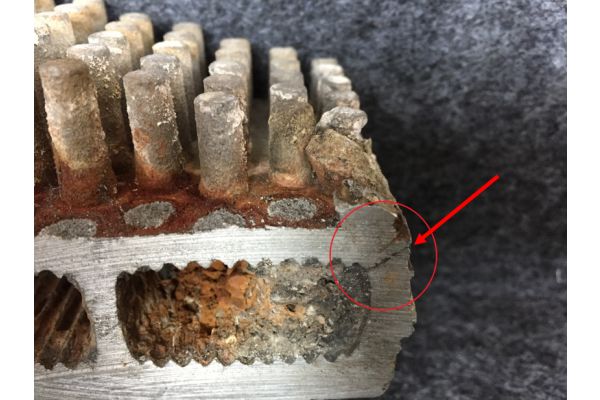
由铝合金制成的有缺陷的发热体,由于腐蚀产物和石灰石被冲洗而局部过热和破裂。
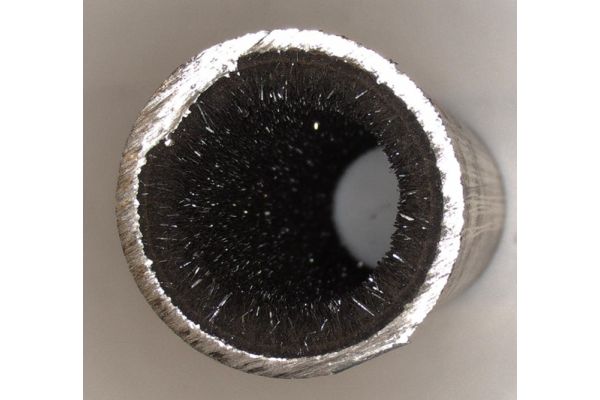
具有磁铁矿和碳酸钙(文石)结晶涂层的永久贸易碳钢管,这是由于与较高的氧气输入有关的相对较高的残留硬度所致。
如果没有氧气,则该腐蚀过程将停止。
热水电导率
在腐蚀过程中,正Fe 2+和负OH-离子都会进入水中。它们的电荷补偿是通过水进行的,并且因水的电导率增加而受到青睐。除此之外,低电导率还阻碍了金属表面上的所有其他电化学过程。
热水的pH值
首先,pH值决定了是否可以在金属上形成顶层。该图显示了铁,铜和铝材料的pH范围,在其中形成了所谓的腐蚀产物钝化层,该钝化层至少在很大程度上抑制了进一步的表面腐蚀:
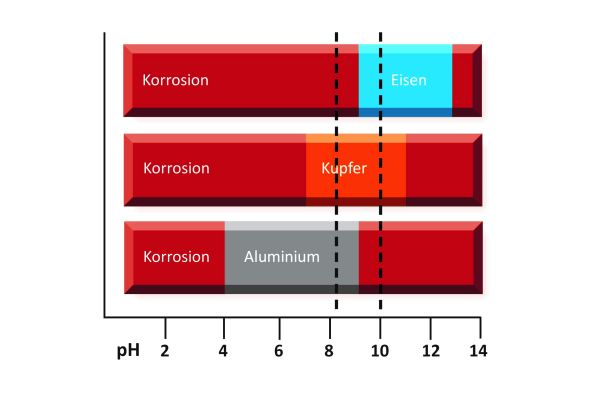
黑钢(铁),铜和铝的主动和被动腐蚀的永久贸易pH范围。垂直线根据现有技术(VDI 2035)限制了热水中要遵守的面积。
作为对安装在加热回路中的金属的最佳折衷,相关规定(尤其是VDI 2035)要求的pH范围为8.2至9.0。
但是,对于不含铝成分的系统,pH值应选择在9.3和10.0之间,这不仅是因为铁的被动行为,而且还因为金属表面上的氧气减少量取决于pH值和较低的pH值更容易流失。此外,在pH值<6.0时,酸腐蚀作用越来越多,H +离子开始脱离作为氧化剂的氧。如此低的pH值在加热水中的抗冻剂残渣已降解为酸的情况下并不罕见。
硬度
热水中残留的硬度很少,对氧腐蚀具有根本上的积极影响。这是由于这样的事实,氧的还原碱化的金属表面(形成OH的- ,见上文),由此碳酸结合那里。
如果水中有溶解的石灰,它将沉积在碱化的金属表面上,从而阻碍或换句话说:抑制进一步的反应。对于中性水,此效果尤为明显。在腐蚀化学方面,碳酸钙在这里用作所谓的阴极腐蚀抑制剂。无需提及的是,与阳极抑制剂相反-可能的剂量不足-没有增加的局部腐蚀现象。
总而言之,这意味着在水侧使用尽可能高的pH值的低盐操作代表了可能的最佳腐蚀防护,但在大量氧气进入的情况下并不能提供任何真正的防护。如果氧气的引入不能通过其他技术措施来控制,例如通过系统分离的方法,则可以考虑直接结合氧气或在热水中使用腐蚀抑制剂。
氧气消耗盒
由于耗氧滤筒是市场上尚未提供的新产品,因此应对此进行详细说明:使用这种类型的“滤筒”,溶解在水中的氧气可以在流过时直接消除。但是,该过程取决于水温。如果加热系统通过这种滤筒重新注满冷水(可能与脱盐或软化结合使用),则可直接从注水中抽出80%的氧气。从逻辑上讲,所形成的腐蚀产物减少了80%,这些腐蚀产物可能例如占据了地板下加热歧管的“顶部仪表”。氧气消耗盒是放置在处理单元的前面还是后面无关紧要。
这种过滤方法注定要在分流加热操作期间使用,从而从40°C的水温高速消耗氧气到<0.02 mg / l的残留浓度。在最简单的情况下,可以使用波纹不锈钢管和所谓的“ taco setter”将这种滤筒安装在回水和进水(吸水侧!)之间。与永久安装的模块(用于部分流脱盐)相结合,该解决方案在技术上更加优雅。
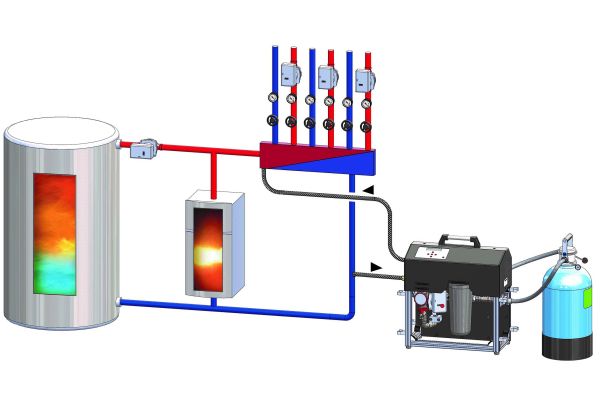
“ permaLine”系统,用于加热水处理,而不会因连接的“ PS 21000IL”脱盐滤筒而中断操作。使用此系统,可以向下校正太高的pH值并消耗掉剩余的氧气。
在这里,水可以连续进行机械过滤,也可以进行时间控制,并除去残留的氧气。如有必要,也可以根据系统水的电导率自动打开脱盐滤筒。
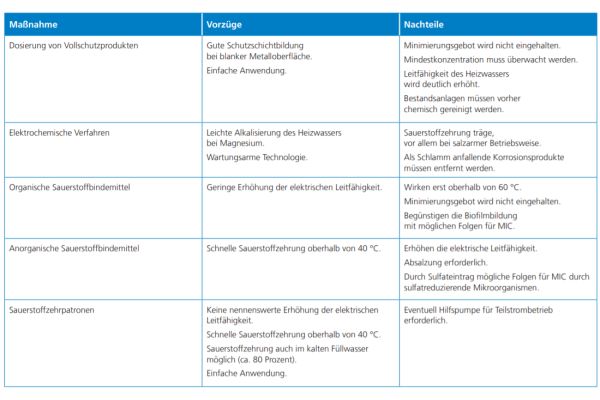
水侧防氧腐蚀保护措施的优缺点(MIC =微生物诱导的腐蚀)。